Aerosols |
|
An
aerosol is a system consisting of very finely divided liquid
or solid articles of dispersed in and filled by gas. In recent
years aerosols have become well known products discharged
from spray dispensers, and the term aerosol has, in popular
speech also come to means the dispenser itself i.e. a pressurized
container made of metal or glass and provided with a discharge
valve, which may be a spray valve or a foam valve. It is filled
with the product to be sprayed and the propellant gas under
pressure.
|
|
The
aerosol can was invented in 1926 by Erik Rotheim. He invented
the first aerosol can and valve that could hold and dispense
products and propellant systems. This was the forerunner of
the modern aerosol can and valve. The patent was sold to a
US company for 100,000 Norwegian kroners, but it wasn't until
1941 that it was first put to good use by Americans Lyle Goodhue
and William Sullivan. They turned it into an instrument for
the US military to fight the malaria mosquito in the Pacific
during World War II. Aerosol spray products have three major
parts; the can, the valve and the actuator or button.
|
|
The
term aerosol derives from the fact that matter floating in
air is a suspension i.e. a mixture in which solid or liquid
or combined solid-liquid particles are suspended in a fluid.
To differentiate suspensions from true solutions, the term
sol evolved originally meant to cover dispersions of tiny
particles in a liquid. With studies of dispersions in air,
the term aerosol evolved and now embraces liquid droplets,
solid particles, and combinations of these. An aerosol may
come from sources as various as a volcano or an aerosol can.
|
|
|
|
The
product to be dispersed as an aerosol may have the liquefied
propellant mixed with it in the form of a solution (Fig.1).
Alternatively, the propellant may be present as a separate
gaseous phase in the dispenser, in which it does not mingle
with the product (two-phase system: Fig.2).
|
|
An
example of the first type is afforded by hair spray. The spray
or lacquer, usually dissolved in alcohol, is completely miscible
with the liquefied propellant. When the valve button on the
dispenser is pressed, the propellant vaporizes immediately,
and its pressure forces the liquid out of the nozzle. The
liquid i.e., the lacquer solution is discharged as a fine
mist. The most commonly employed propellants are chlorinated
hydrocarbons, butane, propane, isobutane, vinyl chloride and
nitrogen. Nitrogen is used particularly for products that
on no account be contaminated in flavor or smell e.g., toothpaste
packaged in aerosol dispensers.
|
|
|
|
Aerosol
toothpaste is an example of the second category of aerosol
systems particularly, the two-phase system in which the propellant
gas forms a separate layer over the product to be discharged.
The dispenser is half milled with nitrogen or some other suitable
gas and half with the product. The pressure in the dispenser
is about 6 to 8 atm. (90 to 120 lb. /in2). Nitrogen can also
be used as the propellant for foods packaged in aerosol form
e.g., cheese spreads, malt extracts, vitamin preparations,
syrups, pudding sauces, whipped cream. |
|
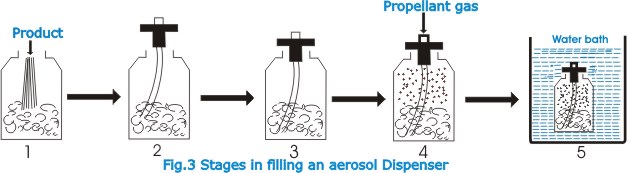 |
|
Filling
an aerosol dispenser at the factory is a simple operation
(Fig.3: stages 1 to 5). First the product is introduced into
the dispenser. This is done by a pneumatic filling machine.
Then the aerosol valve is placed on the dispenser. In the
next stage the valve is force-fitted under high pressure into
the neck of the dispenser, so that a strong gastight seal
is formed between the latter and the valve unit. The propellant
gas is now forced into the dispenser. Finally, the dispenser
is immersed in water to test it for possible leakage, which
is manifested by escaping bubbles of gas. |
|
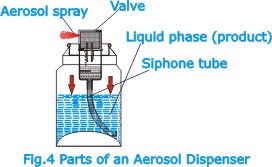 |
|
Aerosols
are coming into increasingly widespread use in industry. They
are used for the disinfection of milk tanks. For this purpose
a spraying device is used which draws the disinfectant solution
by suction from a container and disperses it as an aerosol
by means of two atomizing discs. These discs rotate, and their
centrifugal action sets up a suction which draws the disinfectant
forward through the hollow shaft of the motor. |
|
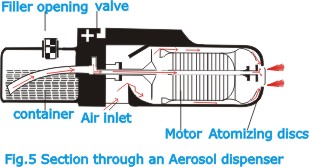 |
|
To
make the aerosol mist flow in the desired direction, a second
air stream is needed. A turbine is installed behind the motor
sucks in air, which flows along the motor and emerges from
the annular aperture around the atomizing discs. This stream
of air carries along the aerosol particles of disinfectant
(Fig.5). |
|
o
DISCLAIMER o
CONTACT US |