Foam Plastics |
|
One
of the basic features of foam-type materials is the structural
configuration of the cells. Absorbent cotton (cotton wool),
felt and glass wool, for example, do not belong to this category
of materials; sponges and cork, on the other hand, do. A difference
can be made between true and false foams. In true foam the
individual cells are not mere relatively thick-walled cavities
or pores, but are separated only by thin partitions and are
interdependent for their stability (Fig.1).
|
|
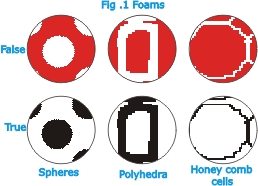 |
|
The
mechanical strength is the highest in the case of foams with
closed (nonintercommunicating) cells. Since no convection
is possible in such materials, they possess good thermal insulating
capacity. With open (intercommunicating) cells the mechanical
strength and thermal insulation are lower; while, these materials
have a high sound-absorbing capacity and are therefore good
acoustic insulators.
|
|
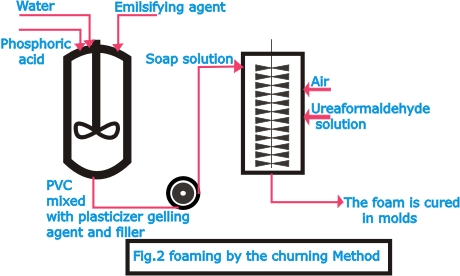 |
|
Artificial
foam materials, including more particularly foam plastics,
can be manufactured by three different methods: by churning
(Fig.2), by expansion with chemical agents (Fig.4) and by
physical methods (Fig.3). The initial materials that can suitably
be processed into foams include polyvinyl chloride (PVC),
polystyrene, urea and formaldehyde condensation products,
and natural synthetic rubber. In the churning process of producing
foam rubber, latex to which fillers, vulcanization accelerators
and foaming agents i.e. surface-active substances have been
added is stirred with air to form foam, which sets and is
then vulcanized with hot air (Dunlop process).
|
|
 |
|
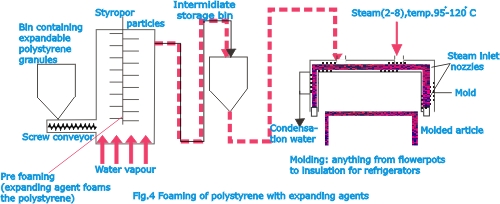 |
|
Urea-formaldehyde
foams are made by foaming a soap solution with an incompletely
condensed water-soluble resin resolution and air in an impeller-type
high-speed mixer. Further condensation is brought about by
the addition of acid. In the process based on physical methods,
the foaming (expanding) action is produced by gases such as
nitrogen, carbon dioxide, or pentane. Gas dissolved in the
material under pressure is liberated from the solution and
thus forms bubbles in the material when the pressure is reduced;
this is the foaming action.
|
|
For
example, PVC pastes are processed with carbon dioxide at a
pressure of about 20 atm. (300 lb. /in 2) and a temperature
between –5oC and 0oC. The fluid mass is passed into
the heating zone of the installation. Here the dissolved CO2
escapes and thus foams the material. The foam sets at a temperature
of 150 oC and is solidified by cooling. Polystyrene is foamed
with pentane, which is added at the polymerization stage e.g.,
in the manufacture of styropor.
|
|
|
|
Chemical
foaming methods are based on the fact that certain substances
will, on being heated, decompose and liberate gas, which forms
small bubbles i.e. foam cells. Azo compounds, N-nitroso compounds
and azides are employed as foaming agents. What all these
compounds have in common is that they liberate nitrogen when
they decompose. For the manufacture of polyurethane foam plastics
e.g., the German product named Moltopren, compounds containing
hydroxyl groups of high molecular weight are mixed with disocyanates
and water. |
|
The
foam plastic is formed according to the equation
|
|
HO.R1.OH
+ OCN.R2.NCO ->… CO2.R1CO2.NH.R2NH.CO2.R1.CO2…
Surplus isocyanate groups react with the added water and CO2
is evolved, which acts as a foaming agent:
R-NCO + H2O -> R-NH2 +CO2
Isocyanate amine
|
|
The
reaction mixture is cast in molds in which both the foaming
and the hardening process take place. Blocks of foam are cut
up into slabs or sheets by cutting machines.
|
|
In
the building industry foam plastics have achieved importance
as heat and sound insulating materials. They are also used
for a number of other purposes e.g., as paddings, packing
materials, materials for the manufacture of sponges and bath
mats.
|
|
o
DISCLAIMER o
CONTACT US |