Plastics Processing |
|
The
properties of plastics and the many different requirements
depending on finished products made from them have led to
the development of a number of methods for shaping and molding
these materials. From the manufacturers who synthetically
produce plastics for industrial use the fabricating industry
obtains the specified initial materials, i.e., the appropriate
polymers with or without the requisite additives. |
|
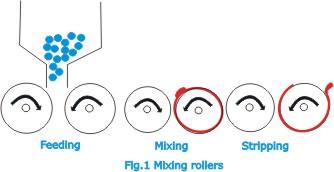 |
|
In
the latter case the user will have to add auxiliary materials
such as plasticizers, stabiliziers, pigments and fillers.
Batch mixing of powdered ingredients is performed in agitators
or mixing drums. Alternatively, kneaders or mixing rolls (Fig.1)
are used for plastifiable materials. The last mentioned device
comprises a pair of rollers which revolve in opposite directions
and which can be heated or cooled as required. |
|
The
material entering the gap between the rollers is squeezed
and mixed. On completion of this treatment the so-called rough
sheet is stripped from the rollers (Fig.1) and passed to a
further stage of processing. Continuous mixing is performed
in extruders, which offer the additional advantage of filtering
the plastics before they undergo further processing (Fig.4). |
|
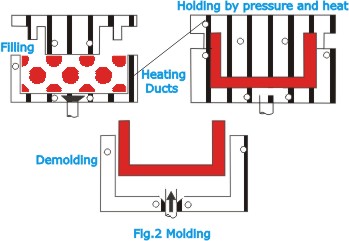 |
|
The
shaping of plastic articles and components without the application
of pressure is effected by casting. The simplest method of
shaping in conjunction with pressure is by molding (Fig.2),
which is suitable for both thermosetting and thermoplastic
compositions. Thermoplastics can be softened by the application
of heat; thermo setting plastics undergo chemical change under
the action of heat and are thereby converted to infusible
masses which cannot be softened by subsequent heating. |
|
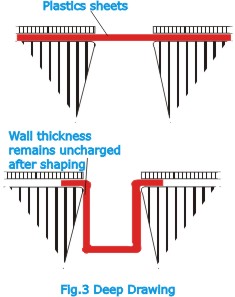 |
|
The
Plastic Processing programme has been drawn up by the Finnish
plastics industry, the universities and Tekes with the aim
of improving the competitiveness of companies developing injection
moulding, and manufacturing and using injection-moulded components.
The programme is finished. |
|
The
aim of the entire programme was to improve the competitiveness
of the companies in the business chain. This was achieved
by speeding up the product development process, the mould
manufacturing process and making them more efficient and by
controlling the production process considerably better than
at present. An additional goal was to improve mould performance,
speed up start-up times for production processes and minimize
environmental impacts. |
|
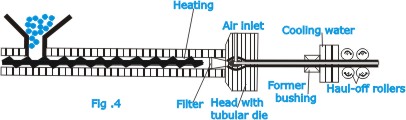 |
|
Another
method of producing molded articles is by injection molding
(Fig.5), which has the advantage over ordinary molding that
preheating, plasticizing, and shaping are done by the same
machine. The only materials suitable for injection molding
are thermoplatics of high fluidity. The granules are introduced
through a hopper into the cylinder, in which they are heated-by
means of a heating jacket- to above their softening point.
A moving piston plasticizes the material and forces it through
a nozzle into the mold. The plasticizing action can be enhanced
by the use of a screw instead of a piston (Fig.6).
|
|
|
|
Articles
or components can also be shaped by the machining of semifinished
products films, sheets, rods or tubes. Machining is more particularly
employed in cases where the articles are of complex shape
or where only a small number are required. Whereas thermosetting
plastics can be shaped only by machining (milling, turning,
cutting, drilling) once they have hardened, semifinshed thermoplastic
materials can be shaped by heating and joined by welding.
Hot shaping of thick sheets can be effected by bending or
drawing (Fig.3). In the drawing process the material to be
shaped is gripped, heated and deformed to the desired shape.
If the wall thickness must remain constant, the sheet must
be resiliently gripped; with so-called stretch forming a reduction
in wall thickness occurs. |
|
In
recent years shaping by the vacuum process has gained importance.
In the female-mold method or negative mold method, the heated
plastic sheet is laid on a concave mold and subjected to further
heating. Air is extracted through holes in the mold, so that
the sheet is drawn by suction into the mold. For the molding
of complex components the plate is prestretched before the actual
negative molding operation begins.
|
|
Alternatively,
a convex master model may be used, in which case the process
is known as the male-mold method or positive-mold method. The
preheated sheet is placed over the master model and preformed.
When the air is evacuated, the desired shape is obtained. The
molding techniques are schematically illustrated in Figs.8 and
9.
|
|
Endless products such as sections, sheet, strip and thin are
produced by extruders (Figs. 4 and 6). Extrusion consists
in forcing a plastic material through a suitably shaped die
to produce the desired cross-section shape. The extruding
force may be exerted by a piston or ram (ram extrusion) or
by a rotating screw (screw extrusion) which operates within
a cylinder in which the material is heated and plasticized
and from which it is then extruded through the die in a continuous
flow.
|
|
Different
kinds of die are used to produce different products e.g.,
blown film formed by blow head for blown extrusions, sheet
and strip slot dies and hollow and solid sections i.e. circular
dies. Wires and cables can be sheathed with plastics extruded
form oblique heads. The extruded material is cooled and is
taken off by means of suitable devices which are so designed
as to prevent any subsequent deformation.
|
|
For
the manufacture of large quantities of film or thin sheet, the
sheeting calender is employed (Fig.7). The rough sheet from
the two-roll mill is fed into the gap of the calender, a machine
comprising a number of heatable parallel cylindrical rollers
which rotate in opposite directions and spread out the plastics
and stretch the material to the required thickness.
|
|
The
last roller smoothes the sheet or film thus produced. If the
sheet is required to have a textured surface e.g., to resemble
wood graining, the final roller is provided with an appropriate
embossing pattern; alternatively, the sheet may be reheated
and then passed through an embossing calender. The calender
is followed by one or more cooling drums. Finally the finished
sheet or film is reeled up.
|
|
Another
field of application consists in coating a supporting material
e.g., textile fabrics, paper, cardboard, metals, various building
materials with plastics for the purpose of electrical insulation,
protection against corrosion, protection against the action
of moisture or chemicals, providing impermeability to gases
and liquids, or increasing the mechanical strength. Coatings
are applied to textiles, foil and other sheet materials by
continuously operating spread-coating machines (Fig.10).
|
|
A
coating knife, also known as doctor knife ensures uniform spreading
of the coating materials in the form of solutions, emulsions
or dispersions in water or an organic medium on the supporting
material, which is moved along by rollers. The coating is then
dried. Alternatively, the coating applied to the supporting
material may take the form of film of plastic, in which case
the process is called laminating.
|
|
Metal
articles of complex shape can be coated with plastics by means
of whirl sintering process. The articles, heated to above
the melting point of the plastics, are introduced into a fluidized
bed of powdered plastics a rising stream of air in which the
powder particles are held in suspension, whereby a firmly
adhering coating is deposited on the metal by sintering.
|
|
o
DISCLAIMER o
CONTACT US |