Zinc |
|
The
chief ore zinc is sphalerite (ZnS), also known as the zinc
blende, which usually occurs in association with galena (PbS)
and smaller quantities of other metallic sulphides. Concentrates
with more than 50% zinc are produced by flotation. From these
the zinc can be obtained by various thermal reduction processes
or by leaching and electrolysis. In every case the process
must be preceded by complete roasting to convert zinc sulphide
into zinc oxide and thereby make it leachable or reducible
with carbon. |
|
The
name of the metal zinc is unusual and, while vague in origin,
was probably first used by Paracelsus, a Swiss-born German
chemist, who referred to the metal as Zincum, in the 16th
century. These words in German apparently mean "tooth-like,
pointed or jagged part" and, as zinc metallic crystals
are needle-like, the derivation appears plausible. Zinc mines
of Zawar, near Udaipur, Rajasthan, were active during 1300–1000
BC. There are references of medicinal uses of zinc in the
Charaka Samhita (300 BC).
|
|
The
Rasaratna Samuccaya (800 AD) explains the existence of two
types of ores for zinc metal, one of which is ideal for metal
extraction while the other is used for medicinal purpose.
Because of the low boiling point and high chemical reactivity
of this metal (isolated zinc would tend to go up the chimney
rather than be captured), the true nature of this metal was
not understood in ancient times.
|
|
From
low-grade zinc ores and from intermediate products containing
zinc, such as flue dusts from lead and copper smelting, it
is possible to obtain zinc oxide by the so-called rotary process;
the material containing zinc is heated under reducing conditions
in a long rotary kiln i.e. a tubular cylindrical furnace which
is inclined and revolves on its longitudinal axis; the raw
material is fed in at the upper end and gradually makes its
way down to the lower end, acquiring a progressively higher
temperature on the way.
|
|
In
the kiln the zinc is volatilized; in the upper part the zinc
vapor is burned to zinc oxide, which leaves the kiln along
with waste gases and is collected in a bag-filter plant. Zinc
production by dry processing presents particular difficulties
because zinc has a low boiling point (906 oC) and therefore
occurs only in gaseous form at the temperature necessary for
effecting the reduction (1300oC).
|
|
|
|
For
this reason reduction has to be carried out in closed vessels
or furnaces in which the zinc vapor can be condensed in the
absence of air. For thermal reduction the concentrate is roasted
a treatment that may be carried out in two stages multiple-hearth
furnace followed by sintering on a traveling grate or in a
single-stage operation in which a proportion of the roasted
material is fed back to the sintering machine. Sintering is
necessary for transforming the material into suitable lumps
to allow air to flow through it during the subsequent reduction
process.
|
|
Reduction
of the zinc oxide can be done by various methods. In the so-called
standard process, reduction is effected in horizontal retorts
in a retort furnace or distilling furnace (Fig.2), which comprises
a lower part containing regenerative chambers for preheating
the gas and combustion air and an upper part in which retorts,
arranged in tiers one above the other, are heated by the hot-flame
gases. A retort of this kind is a rectangular distilling vessel,
about 6or 7ft. long and about 1 ft. square in cross section.
It is made of fireclay and has only a short service life,
having to be renewed every four to six weeks.
|
|
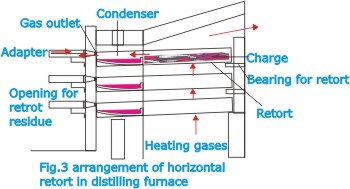 |
|
The
zinc vapor escapes from the retorts and is collected in the
condensers as liquid metal. At the end of about 20 hours the
process has been completed; the liquid zinc and zinc dust
are then removed from the condensers, and the residual matter
is removed from the retorts by special machines. Cleaning
out the retorts and recharging them takes about 4 hours, so
that the whole cycle can be repeated every 24 hours. In a
more recent development of the process a single large condensing
chamber is used instead of individual condensers.
|
|
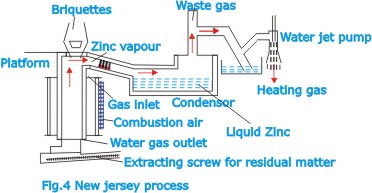 |
|
In
the New Jersey process (Fig.4) reduction is effected in large
vertical retorts about 14m (45 ft) high and of rectangular
cross section, lined with silicon-carbide bricks in the hottest
parts. The advantage over the horizontal retort method is
that reduction can be performed as a continuous operation.
The charge consist of briquettes made of a mixture of zinc
oxide material (roasted blende) and bituminous coal. The briquettes
are fed automatically to the resort, the residual matter being
extracted by a screw conveyor at the bottom. The mixture of
carbon monoxide and zinc vapor is discharged from the top
of the retort into a condenser, where the metal is precipitated
in liquid form.
|
|
There
have been many attempts to utilize electricity for the smelting
of zinc. The St. Joseph Lead Co. (U.S.A) has developed a successful
method of reducing zinc in an arc furnace (Fig.5). The process
is similar in principle to the retort method, except that
the heat is now supplied by the electric arc. Another fairly
recent development is the method employed at Avonmouth (Great
Britain), which has significantly affected the metallurgical
processing of lead as well as zinc.
|
|
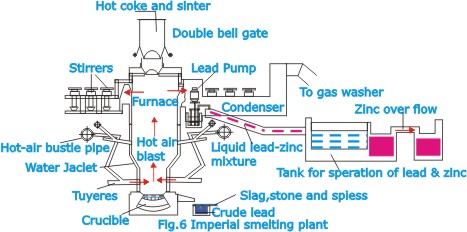 |
|
In
this method, known as the Imperial Smelting process, the two
melts are produced simultaneously from the oxides of zinc
and lead in a shaft furnace. The process is especially valuable
for dealing with ores in which sphalerite and galena occur
in intimate association with each other. The furnace is charged
with coke and a mixture of roasted lead and zinc ores, prepared
by a pressure sintering process. In the furnace, which is
really a form of blast furnace, the lead oxide is reduced
to molten metallic lead, which collects at the bottom.
|
|
The zinc
oxide is likewise reduced and forms zinc vapor, which is extracted
at the top of the furnace along with the combustion gases.
The vapor is passed to a condenser in which the cooling medium
is molten lead, in which the zinc dissolves. The zinc-in-lead
solution is then passed into a separator in which on cooling,
a layer of liquid zinc forms a top of the lead (this separation
is due to the fact that the solubility of zinc in lead diminishes
at the lower temperature). The lead is returned to the condenser,
and the zinc is further processed by refining.
|
|
The
lower part of the first column is heated. Impure zinc is fed
continuously into the top of the column and is vaporized as
it flows down through the heated trays. After further purification
by refluxing in the upper part of the column, the zinc vapor
(still containing cadmium but free of other impurities) is
passed to a condenser, whence it is fed to the top of the
second column, in which all the cadmium is driven off. Zinc
of 99.995% purity is condensed and drawn from the bottom.
Another widely used method of zinc production is by the leaching
of roasted zinc concentrates with acid and then depositing
the zinc by electrolysis from the solution thus obtained.
|
|
o
DISCLAIMER o
CONTACT US |